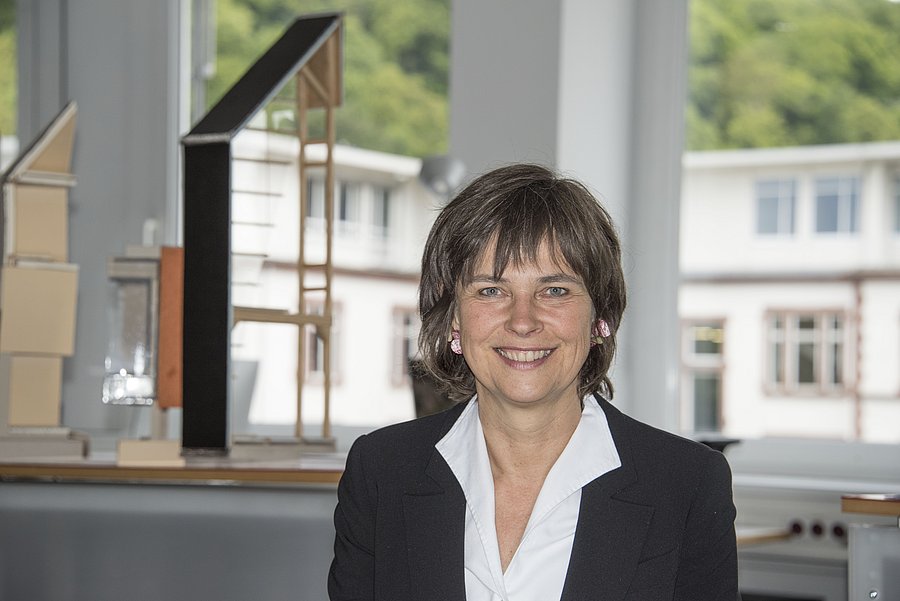
Prof Annette Hillebrandt / Architecture
Photo: UniService Transfer
Realistic visions against the sins of the construction industry
Wuppertal architect Professor Annette Hillebrandt on sustainable, resource-conserving construction measures
Are you still dreaming of building? Make your dreams come true now, we'll build your dream home for you!' You can read these or similar advertising slogans in newspapers or online whenever you think about future property. The fact that Germany already has an anthropogenic stockpile of 50 billion tonnes of materials in goods and waste, and that this stockpile is growing by 10,000 tonnes per person every year, can only be discovered if, like Prof. Annette Hillebrandt, you study the subject intensively. The qualified architect has held the Chair of Building Construction/Design and Materials Science in Wuppertal since 2013 and uses realistic building visions to combat the waste of resources in the construction sector.
Over 50% of all waste in Germany comes from the construction industry
"Over 50% of all waste in Germany comes from the construction industry," says the committed scientist and consciously takes on the David versus Goliath battle because, she says mischievously, "I remember that the right guy won, didn't he?" Such facts are certainly paralysing at first, but the solution must be different, because Hillebrandt is aware of the global scarcity of resources and says firmly: "We simply have to get away from too much waste in the construction sector!" Although she has been a member of Greenpeace for decades, her active rethinking of resource-conserving construction only really came about through research work as part of her professorships when she realised the full extent of the waste. "The aim of our research is to reduce the amount of waste from the construction industry by planning every building project as a subsequent source of resources and constructing it accordingly." The Essen-based company plans buildings so that they are easy to dismantle and the materials can be recycled. To do this, however, the materials must be separated from one another. "Pure means," she says, "that they are not contaminated by other materials. You can visualise this very well with the waterproofing of concrete or masonry basements. The cellar is usually sealed in black against ground moisture. These bitumen seals are usually liquid and soak into the concrete.
However, this contaminates the pure concrete. And this cannot be separated again. Both materials can no longer be separated by type and recycled due to this compound. And so we lose these materials." But that doesn't have to be the case, because Hillebrandt knows, among other things, how waterproofing in basements and flat roofs can also be laid loose and made from recyclable material in a demountable way.
The Friday for Future movement has shown that people can be mobilised to take action, but the dramatic situation in the German construction sector described by Hillebrandt does not yet seem to have reached the public. "The problem is only just entering the consciousness of politicians," explains the researcher. "For years, they have been preoccupied with the energy transition, which everyone now knows about. But a materials transition has not yet been a major topic. The Federal Environment Agency has only recently published a brochure on urban mining. Urban mining means thinking of the city as a mine and recovering raw materials from buildings, infrastructure and consumer goods. This circular thinking is a relatively new topic."
Vintage in the construction sector must not remain a fashion
Rethinking people seems to be the most difficult problem. Clients usually want to build everything from scratch. For Hillebrandt, direct resource conservation also means recycling entire components such as bricks or wooden floorboards. And this is where a current fashion trend comes to her aid. Vintage is the keyword that she hopes will become a permanent trend in the construction industry. "Everyone currently wants a flair of something older in interior design that has patina, feels real and is genuine. It should smell of wood or linoleum, i.e. linseed oil. People find that exciting today. But it must not remain a fashion, it must become mainstream. This trend must become established in terms of conserving resources and avoiding waste."
One argument against the use of used materials is the lack of guarantees that manufacturers only offer for new products. The professor says: "A wooden floorboard, for example, lasts 50, 80 to 150 years without a guarantee anyway. So it's more about having a general knowledge of the material. The value lies in the material itself." In addition, the requirements for components change so quickly due to DIN or EU standards that used components no longer fulfil them within a few years, e.g. because they no longer meet current fire protection requirements or energy saving regulations. They can then only be installed if the building owner bears the risk. "And that's where the difficulty lies at the moment," emphasises Hillebrandt, "legislation also needs to change if we want to waste less."
Who has knowledge of materials?
The topic of the materials revolution is still a long way from being recognised both in politics and among colleagues. "Last year, we published the "Atlas Recycling", in which we visualised our research. I'm currently touring the country and giving a talk once or twice a month to architects, product manufacturers or tradespeople to promote building for the resource or material transition." She objectively states that every architect is literally bombarded with new products and impressive glossy brochures by advertising from the construction industry and can lose sight of the bigger picture as a result. "You really have to look at the list of ingredients in the products. And you also have to read the decimal places. If it contains just a little bit of toxic material, then it's not only harmful to health from a building biology perspective, but it's also no longer recyclable. Nobody wants to end up with a recycled product that they have to fear contains toxins." She is referring to existing laws that do not apply. For example, the Circular Economy Act, "which states that the federal government could (actually) ban new products if they are difficult to recycle or if they contain harmful substances. But the law is not pursued, it is not enforced." The committed academic is annoyed by such lip service, because "this repeatedly creates problems such as the asbestos glut that we are still suffering from. With every remodelling project, we first take asbestos samples. The cheap material was everywhere. In the screed, in the plaster, in the paint. You can't touch a house from the 1960s to the early 1990s without being sure that there's no asbestos in it. And this material always has to be disposed of professionally and expensively. The next problem was only recently imposed on us by the construction industry in the form of external thermal insulation composite systems. Many people have insulated their homes as part of the energy transition and may have opted for plastic insulation instead of mineral insulation because it is cheaper. But every plastic product is made from petroleum, which means it burns well. When it then became clear that this might be a danger for the city, a fire retardant was added to make this cheap polystyrene suitable, i.e. to make it fire-retardant contrary to its original material properties (made from petroleum). This fire retardant, known as HBCD, is toxic, persistent, accumulates in living organisms and can now be found all over the world. Mineral wool, glass wool or foam glass, for example, would be inherently incombustible due to their original properties and would not need to be treated with fire retardants." With the appropriate knowledge and transparency about the ingredients, this plastic insulation material would never have been used. The flame retardant was only banned (with exceptions) in 2016. "These are sins by which the construction industry stands in the way of healthy living and the recycling of materials. That's why legislators need to enforce the laws they already have."
And every citizen can also do their own research. "As a builder, it's always worth visiting the website of the Federal Environment Agency. You can find out a lot of information there."
Urban Mining Award
At her department, Hillebrandt works primarily with young students who compete with other universities in the urban mining competition she initiated. She proudly explains: "We've already had several prize winners from the BUW!". The most important aspect of the Urban Mining Student Award is "that you can dismantle everything again. It is also good if used components or recycled old materials have already been used. You have to be able to dismantle constructions and separate components and materials from each other. Things must not be glued together, they must be loosely clamped, plugged or weighted, and the materials must be recyclable." In addition to all metals, renewable raw materials such as wood, flax, cork or hemp are particularly suitable. However: "The natural cycle is only closed if these renewable raw materials are grown in a sustainable way so that more is never harvested than grows back." She emphasises once again: "If the single use of a material leads to its irretrievable loss, we must not use this material in the first place."
Buildings as interim storage for raw materials
For Hillebrandt, urban mining-friendly construction has the following advantages. "Let's say you have metal cladding on your house, aluminium or galvanised steel panels, which you can resell to the scrap trade. Or you have used expensive oak floorboards, which you can also dismantle and sell. High-quality bricks can also have a sales value. On the other hand, if the house is remodelled or even demolished, the disposal costs for non-recyclable or even hazardous materials are really high. " When asked whether waste from the construction sector is a modern phenomenon, the scientist replies "Yes, 200 years ago there was no waste at all. Take the Bergisches Haus: its construction consisted of wood, clay and straw as wall infill and slate slabs as roofing or weather protection for the walls. At the end of the house's life, the wood and straw rotted, the clay could be mixed again and again with water and the stone cladding disintegrated into small pieces. So basically a cycle: earth to earth."
What would a sustainably planned building of the future look like for you?
"Conversion before new construction" is her credo, "it is important that no new areas are used up, because they compete with areas for food or recreation, for example. When new building plots are developed, the buildings should be elevated,
the soil underneath remains untouched, the soil organisms are preserved. Rainwater must not be lost in the sewer, it should ideally be allowed to seep away on the property. Or it can be used beforehand for flushing toilets, for example (so-called grey water use). The building of the future is not only highly thermally insulated, it also generates its own energy on site using photovoltaics or geothermal probes. And it offers something for nature, giving back what it takes: e.g. through green roofs that hold back rain and bring evaporative cooling to overheated cities or even serve as bee pasture. Facades can also be greened, but they should at least have a light-coloured surface, because dark surfaces get too hot and overheat the microclimate." And the wonderful thing is that these buildings will have a long service life because they are planned flexibly as skeleton structures, i.e. without solid walls. This means they can be easily repurposed. What was planned as a residential building can easily be converted into offices and vice versa if demand changes. At the same time, these buildings can change location, i.e. be rebuilt somewhere else, because they are demotable.".
There is certainly still a long way to go until then, a path that Hillebrandt dares to tread anew every day. If it were up to her, every builder would have clear guidelines. "Anyone who builds a house must ensure that it can be dismantled and recycled at the end. To do this, they must have deposited collateral with the local authority in the amount of the waste they are building, or prove that the property will be a resource after dismantling, which will then require a lower deposit for dismantling and disposal. The investor must be persuaded not to leave investment ruins behind."
After this conversation, you start to think and look at your home with completely different eyes. That's the first step. That's right.
Uwe Blass (interview from 16.05.19)
Prof. Dipl.-Ing. Annette Hillebrandt studied architecture at the University of Dortmund. She then ran her own office for several years and took on her first professorship for Building Construction, Design and Building in Existing Contexts at Kaiserslautern University of Applied Sciences in 2001. She then moved to the münster school of architecture and came to the university of Wuppertal in 2013. There she heads the Chair of Building Construction/Design and Materials Science with a research focus on circular potential in building construction and supports her partner Martin Schneider in their joint architectural practice msah in Cologne.