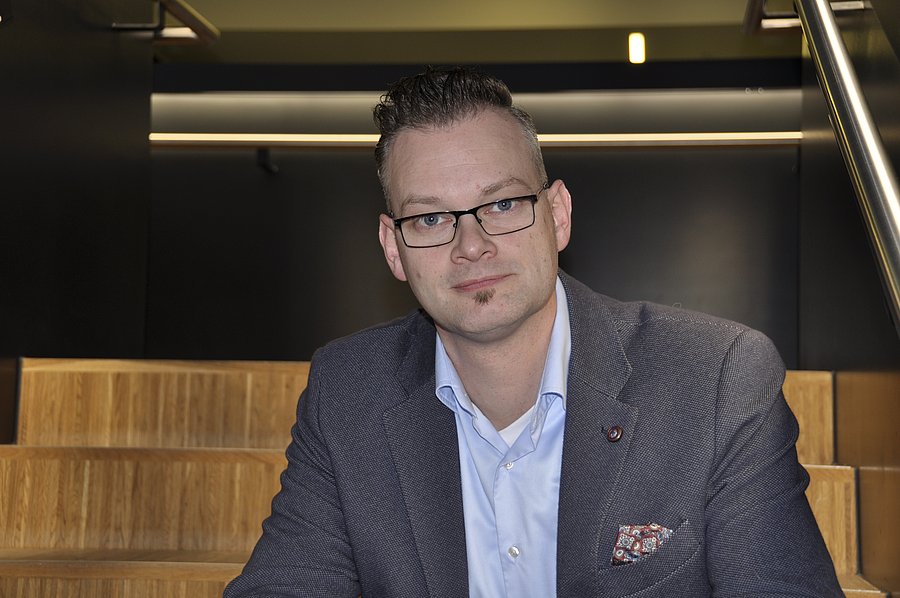
Prof. Dr.-Ing. Manuel Löwer / Product Safety and Quality
Photo: UniService Transfer
"The safety engineer is not the boring man in the white coat"
Prof. Dr.-Ing. Manuel Löwer and the Chair for Product Safety and Quality
"When we talk about safety it usually has a negative connotation," says safety engineer and mechanical engineer Manuel Löwer, owner of the Chair for Product Safety and Quality at University of Wuppertal "because we impose restrictions on the protagonists". And that, the scientist explains, is one of the reasons why schoolchildren and young people in particular have no connection to the subject. "Exactly what pupils and young people do not want is to be patronized by technology and to be hindered from the actual functionality". For this reason, Löwer is increasing his dedication and represents his faculty at job and education fairs where he shows practical application scenarios so that young people can gain access to the subject. "We try to illustrate this at trade fairs via VR on game consoles and 3D printers. We are also showing how you can use design and composition to make products look safer. We are playing a little bit with the understanding and we are clearing up the prejudices". The safety engineer is not the boring person in the white coat, he emphasizes, and in his consultation, he repeatedly asks people to participate in this creative process when it comes to developing and designing new products. He says quite directly: "You can help shape innovations, you are right in the middle of it!"
We take topics that students understand, that they know from daily life
Löwer sensitizes young people with practical examples. For this he sometimes puts a mobile phone on the table and asks his opposite, what he or she would do, if all the functions, which the user considers meanwhile as natural, were suddenly no longer there? "Then they understand, especially with networked systems, that you have to make sure that functionality is simply there in the product," he explains. "We take topics that pupils understand, that they know from everyday life. You can not assume that the topics that are important to us in the corporate context will be understood by pupils. That does not work."
Reorientation of the chair and interdisciplinary work at the institute
Since 2017, Prof. Dr.-Ing. Manuel Löwer has been teaching in the Department of Product Safety at the University of Wuppertal. In 2019 he will also take over the Department of Quality from an emeritus colleague and will now combine both subjects under the Chair of Product Safety and Quality. "Thematically, the subjects are well compatible and there are synergies," he explains, who is also actively involved in Solingen as the Chairman of the Institute for Product Innovations at the university. The declared aim of his research is "to integrate safety and quality as early as possible in the development process, so that we do not have to eliminate errors in the end, but that we do not make them in the first place". Löwer sees the exciting task in Solingen above all in interdisciplinarity. "It is an interdisciplinary institute with members from other faculties. It is basically the central point of contact for taking a holistic view on innovations. We have, for example, our colleague Gust with construction, our colleague Weber with materials and manufacturing processes or our colleague Kalweit from the Faculty of Design and Art. There are a total of six colleagues who integrate themselves with their respective specialist focus."
International product safety using the example of an e-scooter
Löwer is currently working with an automobile manufacturer on the market launch of a new e-scooter. "When companies want to implement something that is completely, totally new, there is usually no experience with it. The risk is relatively high and I have to think about everything that needs to be considered early on before I launch something on the market so that I end up with a safe product and not just meet the legal requirements," he says, describing the laborious process that already starts with an innovative concept because there are different safety requirements at every stage of development. And the safety engineer does not work alone. "Every specialist discipline contributes something to product safety. The mechanical engineer can describe the strength and interaction of components, the electrical engineer ensures, among other things, electromagnetic compatibility and the software developer defines the safety architecture, i.e. each specialist discipline has its own methods or tools. The safety engineer has the superordinate competence to integrate these skills, to fundamentally analyze the product and determine and contain the risk". With regard to the new e-scooter mentioned at the beginning of this article, which was already presented as a prototype at the IAA (International Automotive Exhibition) in September, new problems arise before the market launch, which the safety engineer has to take into account. As Löwer explains: "There is a new act on small electric vehicles, the eKFV. A regulation that has been in effect ever since these scooters have been allowed to be moved on the road. Howeever, for this legal boundary condition there are still no specific technical standards or complex tests as one would expect as a customer." Although it is known that the handlebars should and must have a certain height, a brake is needed and a small license plate has to be attached and that there are basic, generic guidelines for the marketing of products in general, "all this does not make the product inherently safe. What we are now doing in cooperation with this automotive manufacturer is we are defining new test scenarios." The planning is made more difficult by the fact that the standards of an e-scooter have not yet been defined. Löwer must therefore carry out a risk assessment that takes into account all the experience gained and the act on small vehicles that has come into force. "When the vehicle is launched on the market, neither the user nor the traffic must be particularly affected by it" and when all this has been taken into account, it must also be formulated in a legally compliant manner. In the case of the automotive manufacturer, the so-called Declaration of Conformity - a binding declaration that the product has the specific properties and fulfills the legal requirements - is developed for 55 markets worldwide. "It helps that I am well networked internationally," laughs Löwer.
Danger prevention in all production phases
"In production, too, you have to make sure that the product is so safe that the employees who produce it are not endangered," says Löwer, describing the scope of his tasks. This even includes recycling aspects. "You can upcycle old products or their components, i.e. you can make something new out of them, or you can downcycle them, i.e. give them a lower quality grade for applications," explains the Löwer who was born in Wuppertal, "or we have to watch out that we separate materials according to type in order to reduce environmental pollution. Löwer knows from his own experience how difficult it is to place a new product on the market without getting into possible legal difficulties. "The mere use and application of existing standards does not help you, because the more specific the standard is, the faster it becomes obsolete," the expert knows. Product liability reasons can arise, even if one refers to the "local" state of the art. "What do we know about what is currently being realized and sold somewhere in America or China? If you launch a similar product with a lower safety level onto the market here and something happens, things can get very tight. There are also product monitoring obligations that go beyond your own product and include misuse. One must be careful."
Cooperation with top designers from Korea
Löwer's good international network has led to a lively cooperation with Hongik University in Seoul. Interdisciplinarity is also the keyword here. "I got to know the Korean colleagues at a conference of an international project in 2007," reports Löwer, who at that time was responsible for international cooperation with 64 universities at RWTH Aachen University. "We did not have a design faculty back then and Hongik University is one of the world's leading design universities," the German scientist was keen to work with. "At that time, I was responsible for the chassis of an automotive in accordance with the Formula 1 regulations in a project of General Motors, and the Koreans came to me," he explains, because they were enthusiastic about the German engineering sector. "And then, within six months, we set up a completely new course, which I have now been running with them for 12 years. It is a lecture that discusses international collaboration processes between designers and engineers, and we do this using the example of an automotive." The German-Asian team develops vehicle concepts in online courses with final research visits of the students in the respective countries. "I have now also been able to integrate this subject into the curriculum in Wuppertal. In 2019 we were also able to start an exchange program from Wuppertal. The first student flew to Korea for the winter semester. So it is starting as well," says Löwer happily.
Sustainable, natural materials of the future
The issue of sustainability is also making itself visible in the area of product development. Constructing with natural materials could be a trend-setting way forward. With collaborations in the field of botany, especially molecular genetics, causal relationships from the cell to the product are being researched continuously. The Wuppertal scientist is also involved in this area. "At first glance, this sounds quite strange. What does a mechanical engineer, an automotive or safety engineer have to do with natural materials?," he asks himself and spreads out a few plant exhibits in front of him. "A few years ago, we thought about how we could make natural materials usable for mechanical engineering applications. Wood is very well known to the layman in house building, but it also has a weight that has to be taken into account in the mobile sector. Besides, the safety engineer gives into consideration that wood is also always inhomogeneously, thus not evenly developed, because changed water supply or permanent sun exposure changes the natural growth.
Safety factors here are many times higher than in conventional mechanical engineering. The idea of the lightweight construction application was born with bamboo experiments. "The interesting thing about bamboo is that it has primary growth, not a secondary growth. This means that when the shoot comes out of the ground, it keeps its diameter. The tree goes into the breadth afterwards, the bamboo keeps its diameter. We already know how big it will be" enthuses Löwer, "and then we let it grow in shape. So the bamboo is not bent under heat during processing, which could lead to a loss of cell stability and firmness, but it grows purposefully into a given shape. "Then it deposits many more cells at the bottom and becomes much stiffer. I have a constant homogeneous distribution at the top and a cell accumulation at the bottom, so I increase the stability of the component through growth. It no longer buckles, because it has strengthened itself organically." Löwer knows bamboo strains that grow more than a meter a day. With colleagues in Brazil at the University of São Paulo, he works with calabashes, i.e. ornamental pumpkins. They are ultra-light, waterproof and can replace plastics. Löwer has already grown an ornamental pumpkin in the shape of a child's bicycle saddle. "This way we can see which plants can be used for which application horizon," he continues. Mushrooms could also replace plastics in the future. To this end, he is experimenting with oyster mushrooms, some of which develop a shiny surface. "Depending on how we influence the mushrooms, they can also be used directly in the field of vision. Others we have grown into furniture. We then take waste materials from the grain processing industry. These husks, for example, are used by this mushrums as a nutrient and then grow into a form that you simply heat up briefly. The mushrum stops growing and goes into a rigid state. Then you can put it up as furniture and when you do not need it anymore, you throw it on the compost." On the way to CO2-reduced production techniques, these natural materials offer new paths to be taken. Product safety always has to do with responsibility. Löwer sees the responsibility towards the users as an obligation of the economy. This commitment is inherent in the economy of Bergisch Land. "The contacts I have had with the Bergisch economy so far show to me that the companies have understood the signs of the future", says the researcher "security is therefore always one of the essential topics, especially in the utilization."
Uwe Blass (Interview on 26.11.2019)
Prof. Dr.-Ing. Manuel Löwer studied Mechanical Engineering/Vehicle Engineering at the RWTH Aachen. In Wuppertal he has been head of the Chair for Product Safety and Quality since 2017.