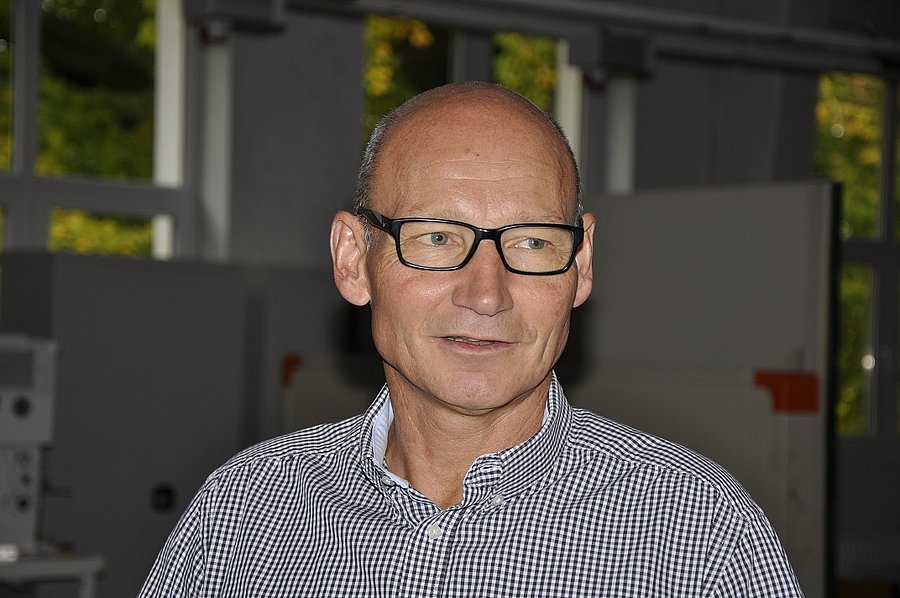
Prof. Dr.-Ing. Ulrich Jung / Digital and offset printing
Photo: UniService Transfer
"I switch on the light and I'm done!"
Prof. Dr Ulrich Jung and UV-curing printing inks in the teaching and research area of digital and offset printing
Time is money... in the printing industry, too, the demands on machines and people are increasing from year to year. Processes have to be constantly optimised, delays lead to losses and competition is immense.
Ulrich Jung, a trained physicist, has been teaching and researching at the University of Wuppertal since 2009. His specialism in the Faculty of Electrical Engineering, Information Technology and Media Technology: digital and offset printing for the research field of printing and media technology.
"Printing processes are actually very old industrial processes," says Jung, but the chemical-physical principles are still not fully understood. This is particularly due to the complexity of the processes. They work so well because a great deal of empiricism can be incorporated. We know from experience how it works, "but for us researchers there are still many large blank areas in our understanding."
"We are researching the physical and chemical relationships that take place in the printing processes, i.e. the offset and digital printing processes."
One economically interesting area of research in this context is the field of radiation curing. Generally, liquid inks are used for printing, but they still need some time to dry. The process of radiation curing - a similar procedure is familiar to the layman from dental technology - has the great advantage that the material illuminated with high-energy UV radiation hardens in less than a second. Jung refers to the ever shorter lead times and marketing campaigns in the packaging industry, for example, and recognises the advantages of this printing process, which enables immediate further processing.
Nevertheless, the radiation-curing printing process is not without controversy, the process control is complex and it is not possible to say with one hundred per cent certainty whether the ink has really dried completely. The chemical process of polymerisation, i.e. a synthesis reaction within the printing ink, can lead to components of the ink diffusing and possibly finding their way into the packaging contents. There were already negative examples from the food industry in the 1990s.
Mineral oil residues in advent calendars
This is why many specialist conferences are also focussing on this topic. The aim is to develop a reliable measuring method in order to be able to certify the desired harmlessness at some point, as the latent risk of diffusion of uncured colour components remains for the time being. Jung cites the example of mineral oil residues in Advent calendars, which can transfer to packaged chocolate. On behalf of the food industry, test persons therefore test chocolate with regard to changes in the flavour of the packaged goods.
Other companies avoid such problems and only use certain types of packaging as a matter of principle. The pharmaceutical industry, for example, works exclusively with transparent packaging. The packaged goods can be seen by the buyer directly in the primary packaging, the so-called blister. Ecologically questionable, this packaging still offers the highest level of safety.
At this point, Professor Jung once again emphasises the importance of interdisciplinary work in this area. "We are not chemists or physicists. We are familiar with the application and understanding of the process and examine it from our technical and methodological perspective."
"Anything that shines is perceived as particularly valuable."
The packaging market is booming. The VDMA (German Engineering Federation) presented market data on packaging printing on the fringes of a trade fair this year. Total global sales of USD 286 billion are forecast for 2020, which corresponds to an increase of USD 44 billion compared to 2015. ***
Jung knows that a lot of waste is produced in the packaging sector in particular, but "anything that shines is perceived as particularly valuable". In the cosmetics sector in particular, packaging shines in competition with each other and is even supplemented with extra film. None of this is good for the environment. "It would be more resource-friendly," says the Limburg native, "to use a lacquer print that only colours where necessary. But the industry will not promote ecological aspects, and a rethink on the part of the public would ultimately be detrimental to the economy," he soberingly concludes.
The Print and Media Technology degree programme was discontinued in 2012 and it is now only possible to study this subject in Wuppertal as a combined Bachelor's degree. "Printing technology is not going to disappear," Jung is certain, "but the attractiveness of entering this industry is extremely low among young people." Nevertheless, the demand is there, and the faculty is also creating a new media degree programme, which will primarily focus on electronic media.
"The system always measures, but the question is whether it measures crap or measures correctly."
Printing presses are becoming ever larger and more complex and now have an integrated inspection system. For example, the quality of the ink is constantly checked during the printing process. Classically trained printers are no longer able to operate these complex machines. Engineers are needed who not only understand how they work, but can also check the measurements as quality controllers.
The barrier coating and the chip bag
The range of printing technology topics in the teaching and research area of digital and offset printing at the University of Wuppertal is almost inexhaustible.
For example, the department offers special lectures on security printing, in which students can acquire knowledge about the security features on banknotes, which can also be applied to tickets or railway cards. On behalf of the Phillips company, Jung investigated conductive copper inks that are printed on glass and, as an alternative to die-cut Braille, worked with an expanding varnish that pops up on contact with printed material. Or he works with barrier varnishes. Anyone who has ever eaten crisps will recognise the best example of this. The inside of the bag is sealed with a metal varnish that guarantees the printed durability and does not let in any oxygen.
His current projects are designed to be ecological. He is working on the reuse of rejects in flexographic printing and on photoluminescent, solvent-free colours that are to be produced with UV inks.
"Products that are printed on are often not printed products."
The printing press industry is no longer growing, Jung knows from his own many years of experience, and one new machine replaces two to three old machines, but the print products are changing. Printed products are created that the layman and customer do not interpret as print products. These include speedometer displays in cars, laminate into which a grain is printed or the large area of decorative printing in the form of tiles.
He wishes his students more time to try things out and concludes: "The future is uncertain, and I don't think young people can even foresee where our students will develop their strengths. Some of them don't even realise what they are really good at during their studies."
Uwe Blass (interview from 13 October 2017)
Prof Dr Ulrich Jung studied at the TH Darmstadt, obtained his doctorate in 1992 at the Institute for Printing Machines and Printing Processes there and worked in the private sector until 2008. In 2009, he joined the University of Wuppertal, where he took over the teaching and research area of digital and offset printing for the research field of printing and media technology.